Our journey to a sustainable tomorrow #2 | Fine tuning and the bigger picture
In the first post of this mini blog series, we gave an overview of the ambitious journey we embarked on in 2023, with the goal of revolutionizing energy consumption at our Vuorela factory. With a clear objective of enhancing energy efficiency, we kicked the project off by meticulously analyzing our current energy solutions and laying out a strategic roadmap spanning from 2023 to 2025. If you haven’t already, we recommend reading the first part of this blog series. You’ll find it at the link below.
But for this blog post, let’s skip to business. The things we discuss in this blog post might seem very simple at first, but like in every aspect of business and life, the road to achieving big things usually lies in the small decisions and tiny steps on the way.
🕸️ Everything works better with good partners
The history of our factory facilities here in Vuorela dates back to the 1980s, and over the decades, our factory building has undergone many expansions, with the latest occurring in 2019. Therefore, as we invest in new technology and modernize our entire energy system, we are once again transforming this building and taking it to a new level. To successfully carry out a project like this, we need a large network of reliable partners. Fortunately, we have just that.
In the first blog post, we briefly mentioned that one of our initial investments was the renovation of our factory’s property automation, centralizing all functions in one system: Honeywell CentraLine. In addition to Honeywell, numerous experts have assisted us and continue to do so in taking the right steps. Like many of our projects, we are collaborating with various domestic and local partners, not only to further our success but also to advance the knowledge and capabilities of our partners. For this project, we have the pleasure of collaborating with various research institutes (e.g., VTT), educational institutions, and local energy companies.
Choosing the right partners and selecting a system like CentraLine, which offers a tremendous range of integration possibilities with multiple systems, is significant as we consider our long-term goals and our commitment to continuing our building’s decades-long journey, taking yet another step forward.
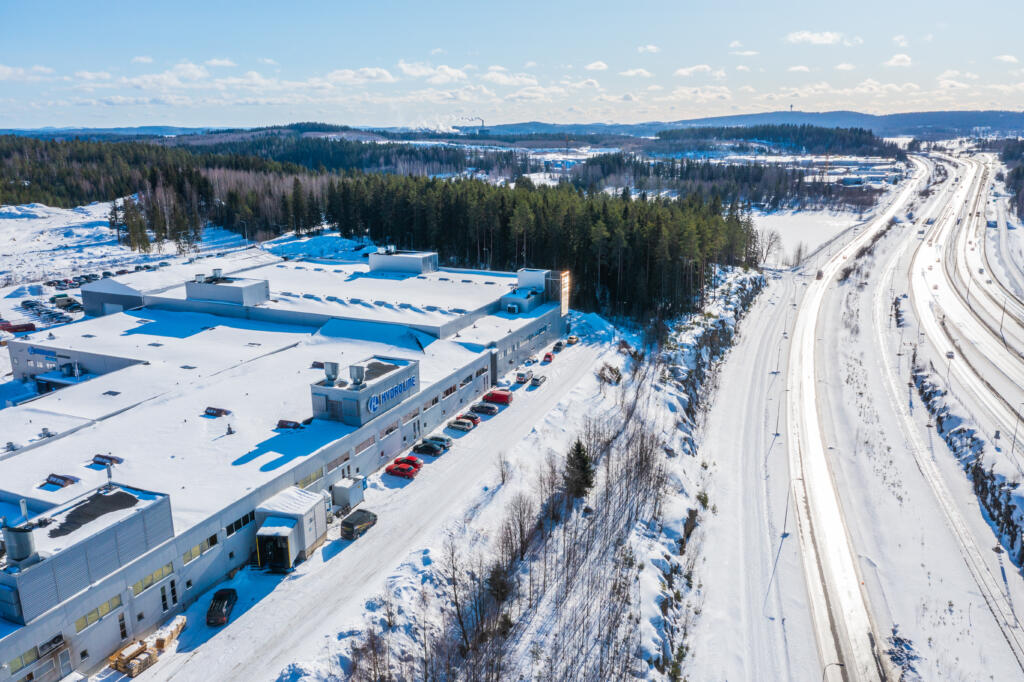
💎 Fine tuning the ventilation…
When it comes to energy management, one step on our roadmap involves fine-tuning our ventilation system. Renewing and integrating the ventilation system into the comprehensive energy management system is a crucial step toward improving energy efficiency and optimizing our production operations. Ventilation systems are vital components of property conditions and production facilities, significantly influencing energy consumption.
Ventilation systems play a pivotal role in maintaining indoor air quality and temperature in factory conditions. In simple terms, a factory’s layout can be likened to a box, with machines on the roof drawing in fresh air from outside through filters and expelling used air from within. Fine-tuning the property’s automation system has enabled refinements in ventilation management. Honeywell CentraLine’s automated controls ensure precise regulation of air exchange, optimizing energy usage and reducing unnecessary consumption.
Understanding the need for ventilation is crucial. It’s not just about maintaining a comfortable environment; it’s about aligning ventilation with usage patterns. For instance, during weekends when the factory is less populated, running ventilation at full capacity is wasteful. Conversely, during peak production hours, ventilation needs to operate efficiently to meet the demands of employees and processes.
Honeywell’s system allows for dynamic adjustment based on real-time data. By analyzing workforce schedules and occupancy levels, ventilation can be optimized accordingly. This level of precision ensures that energy is directed where it’s needed the most, avoiding unnecessary usage during idle periods. For example, if only a fraction of the workforce is present for a specific task on a weekend, ventilation and lighting in that area can be scaled back, resulting in significant energy savings.
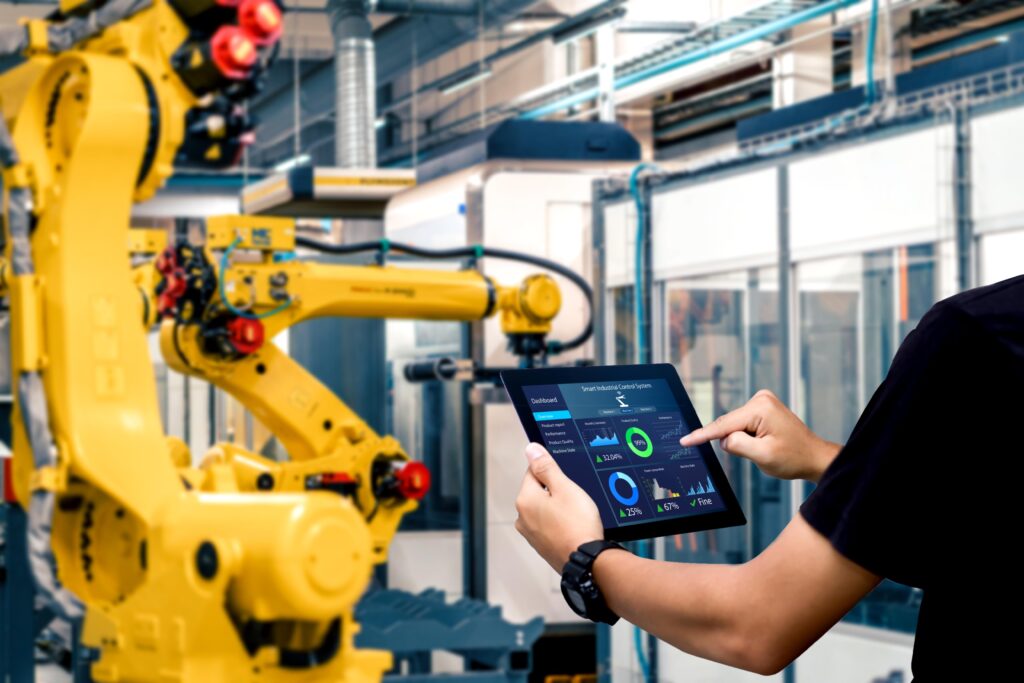
👨🏭… and the compressed air system
Optimizing the compressed air system in a factory, especially in environments where intensive operations like welding are common, is paramount for maximizing energy efficiency and cost savings. Compressed air is often referred to as the “fourth utility” due to its widespread use across various industrial applications. However, its production and distribution can be energy-intensive, making efficient management essential for reducing operational expenses and environmental impact.
One key strategy for optimizing compressed air usage is implementing scheduled shutdowns during periods of reduced production activity, such as weekends. Turning off the compressed air system during these times leads to significant energy savings. For instance, at the Vuorela factory, closing the compressed air system on weekends results in substantial electricity savings and reduces emissions, contributing to environmental sustainability efforts.
Moreover, identifying and repairing leaks within the compressed air system is critical for minimizing energy wastage. These leaks not only lead to inefficiencies but also increase operational costs. Through in-depth investigations, the Vuorela factory has successfully detected and rectified leaks, resulting in impressive energy savings of up to 20%.
Furthermore, adopting on/off control for other production equipment during non-production hours further enhances energy efficiency. By synchronizing the operation of equipment with actual production demands, unnecessary energy consumption can be avoided. The potential savings from implementing such controls, including those for the compressed air system, during weekends can amount to significant cost savings.
🦾Always looking at the bigger picture
Our decision to select a system like Honeywell CentraLine was driven by the desire for greater control and efficiency. With advanced technology, the factory can optimize ventilation and integrate other systems like lighting based on occupancy data. This level of automation and customization ensures that energy is used intelligently, minimizing waste. Tuning and integrating our ventilation into our comprehensive energy management system is a strategic investment. By leveraging advanced automation and real-time data analysis, we can achieve significant energy savings, enhance operational efficiency, and contribute to sustainability objectives.
Moreover, fine-tuning and optimizing the compressed air system are critical aspects of energy management in our Vuorela factory. Implementing strategies such as scheduled shutdowns, leak detection, and on/off controls enables significant energy savings while minimizing environmental impact. These efforts not only contribute to cost reduction but also demonstrate a commitment to sustainable manufacturing practices. Overall, these initiatives reflect our dedication to responsible resource management and pave the way for a more sustainable future.
💎
Stay tuned as we unveil the next steps in our roadmap, exploring cutting-edge technologies and innovative solutions that will further propel us towards our energy efficiency goals. To follow our journey closely and be the first to learn about the upcoming developments, connect with us on LinkedIn. Your support and engagement are crucial as we collectively shape a future of sustainable manufacturing. Together, let’s build a smarter future!
More from our blog 📃
How our automated production line works
26.04.2023
Value Stream 1 (VS1), our automated production line, is one of Hydroline’s most valuable assets. VS1 was launched in September 2019. It is a testament..
Read moreLEO: The predictive maintenance solution for hydraulic cylinders
27.06.2020
What is LEO, the predictive maintenance and monitoring solution for hydraulic cylinders? The project with LEO started already in 2013 when Hydroline presented the invention..
Read moreSavroc TripleHard® chrome coating – revolutionizing sustainability and safety in manufacturing
24.01.2024
In the era where an increasing amount of attention towards environmental responsibility, sustainability, safety, and financial prudence are at the forefront of business considerations, the..
Read moreGravimetric analysis in hydraulic cylinder manufacturing
01.06.2020
Gravimetric analysis in hydraulic cylinder manufacturing process? In our previous blog post, we told you about the hydraulic cylinder assembly and as we mentioned in..
Read more