What is a hydraulic cylinder?
Put simply, a hydraulic cylinder is one of the four key components in a hydraulic system. In these systems, fluid, typically hydraulic oil, is used to transfer energy from a motor to an actuator. That actuator is often a hydraulic cylinder. Hydraulic cylinders are all around us, even if we don’t always notice them. They play a vital role in countless machines we encounter every day: excavators, trucks, forklifts, tractors, aerial platforms, mining equipment… you name it! Despite their wide range of applications, most people rarely stop to think about just how essential hydraulic cylinders are in modern machinery.
🔍 How do hydraulic cylinders work?
A hydraulic cylinder is a type of hydraulic actuator that converts hydraulic energy into linear mechanical motion. In simple terms, it acts like the muscle of a machine. Just as muscles move our limbs, hydraulic cylinders create movement within a machine by pushing or pulling mechanical parts.
Hydraulic cylinders operate within a broader hydraulic system, where energy is transmitted through a fluid, usually hydraulic oil. When the system’s power unit rotates the hydraulic pump, it generates fluid flow, measured as volume flow rate (typically in cubic meters per second, m³/s).
The pressure within the hydraulic system is determined by the load that resists this flow; the load is often often applied by a hydraulic cylinder or valve. This resistance is what allows the system to build pressure, enabling powerful and precise movement.
A key principle behind hydraulic systems is Pascal’s Law, which states that pressure applied to a confined fluid is transmitted equally in all directions. This uniform pressure acts on the surfaces within the hydraulic system, enabling consistent force distribution.
The relationship between force, pressure, and area is defined by the formula:
p = F / A
( p = pressure [Pa or N/m²]; F = force [Newtons]; A = surface area [m²])
In a hydraulic cylinder, this principle is applied to generate linear motion:
When hydraulic fluid flows into chamber A of a double-acting cylinder, pressure builds up and pushes the piston rod outward (F = p × A₁).
To reverse the motion, hydraulic fluid is directed into chamber B, causing the piston rod to retract (F = p × A₂).
This ability to control movement in both directions makes double-acting hydraulic cylinders highly versatile in various heavy-duty applications like excavators, forklifts, and industrial machinery.
⚔️ Single-Acting vs. Double-Acting Hydraulic Cylinders
Hydraulic cylinders are generally categorized into single-acting and double-acting types, depending on the direction of motion they provide.
What is a single-acting hydraulic cylinder?
A single-acting hydraulic cylinder generates motion in only one direction using hydraulic pressure. The return motion happens passively, typically via an external load, a mechanical spring, or gravity.
In some single-acting cylinders, there may not be a piston at all, only a piston rod. Hydraulic fluid is directed into the cylinder, where it applies pressure to the rod’s cross-sectional area, causing it to extend outward.
Common use of single-acting hydraulic cylinders:
Single-acting hydraulic cylinders are often found in, for example, forklift trucks, where the lifting motion is powered hydraulically, and lowering occurs due to gravity. They are also commonly used in dump trucks, hydraulic presses, bale ejectors, car lifts, and clamping mechanisms, where force is only required in one direction and the return stroke can be achieved through load weight or spring tension. Their simple design makes them cost-effective and reliable for repetitive tasks in vertical lifting and holding applications.
What is a double-acting hydraulic cylinder?
A double-acting hydraulic cylinder, on the other hand, uses hydraulic power to move in both directions: extending and retracting. The cylinder includes a piston that separates two chambers (chamber A and chamber B). Hydraulic fluid is directed alternately into each chamber, which pushes the piston and the rod either out or in.
When pressure is applied to chamber A, the piston rod extends (F = p × A₁).
When pressure is applied to chamber B, the piston rod retracts (F = p × A₂).
🧩Anatomy of a hydraulic cylinder
In the picture below, you’ll find the basic structure and the main components of a double-acting hydraulic cylinder.
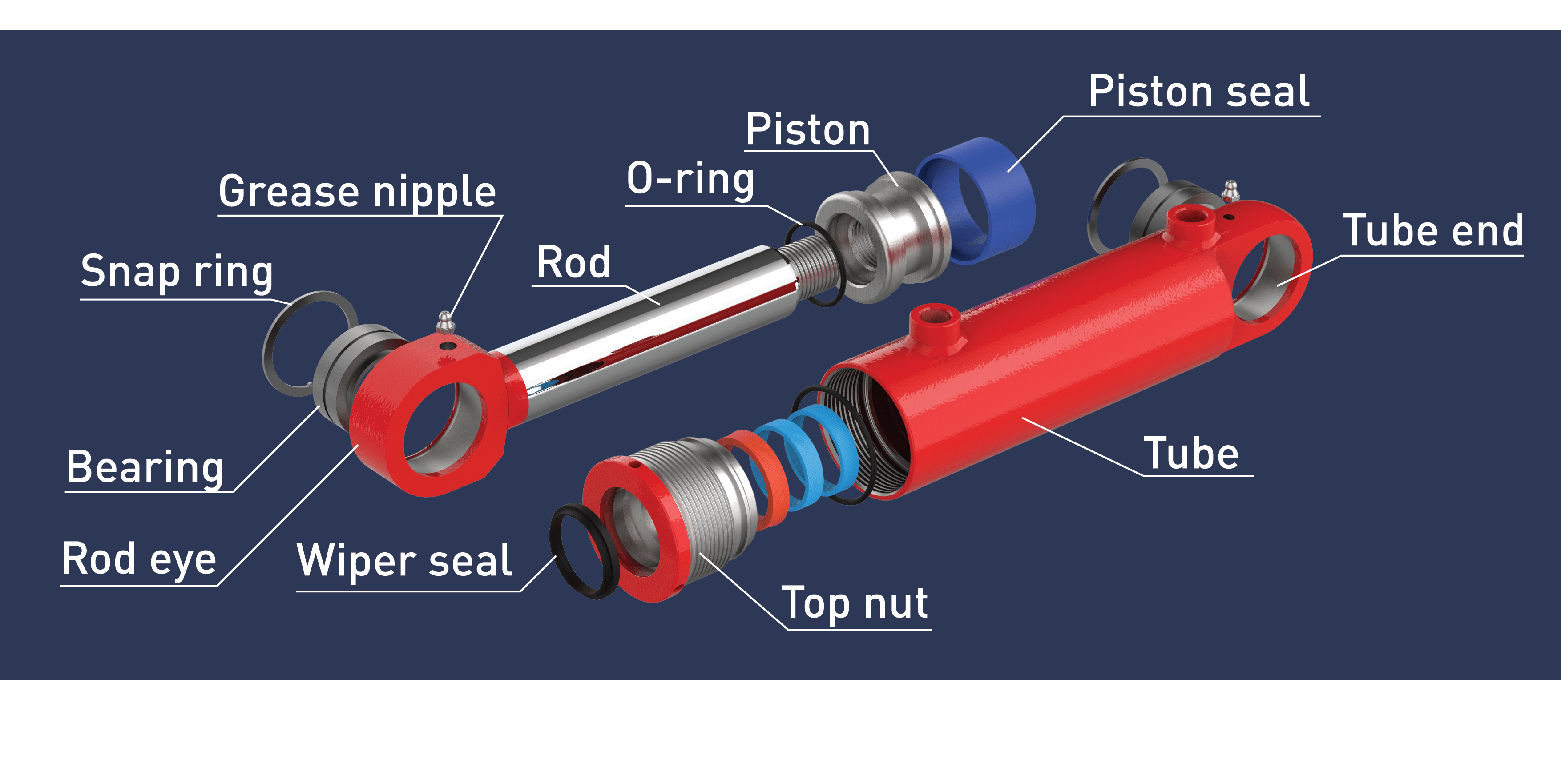
A hydraulic cylinder consists of several key components that work together to deliver reliable linear motion:
- Cylinder tube: The main body housing the internal components.
- Piston and piston rod: Converts hydraulic energy into linear mechanical movement.
- Seals: Prevent hydraulic fluid from leaking and maintain pressure inside the system.
⚙️Role of hydraulic seals
Hydraulic seals are critical for keeping oil in the correct chambers. They come in various types, with the O-ring being the most common. These seals are typically seated in grooves and rely on hydraulic pressure to function. As the fluid flows, it pushes the seal into position, pressing it tightly against the surfaces to prevent leakage. This principle is shared across all pressure seal designs.
🧠 Integrated functions and smart technology in hydraulic cylinders
Modern hydraulic cylinders can include integrated hydraulic components such as:
- Flow control valves
- Pressure relief valves
- Load-holding valves
These integrations enhance performance, safety, and efficiency—especially in complex hydraulic systems.
🤖 Smart hydraulic cylinders: Sensors and predictive maintenance
Today’s smart hydraulic cylinders often come equipped with integrated sensors that monitor key performance indicators such as pressure, piston position, temperature, and operating cycles. These embedded sensors play a critical role in predictive maintenance, enabling operators and maintenance teams to detect potential issues before they lead to costly failures or downtime.
By continuously collecting real-time data, smart cylinders allow users to, for example:
- Monitor hydraulic pressure and applied force, ensuring the system is operating within safe limits and identifying abnormal load conditions.
- Track piston position with high accuracy, which is essential for applications requiring precise motion control or synchronized movement between multiple cylinders.
- Calculate cylinder speed by analyzing position change over time, helping to verify system performance and detect flow-related inefficiencies.
- Measure fatigue and wear by logging stroke cycles, load profiles, and temperature variations—factors that affect the cylinder’s mechanical lifespan.
With Hydroline’s intelligent system, LEO (Lifecycle Efficiency Online), sensor data can be used to assess the cylinder’s real-time condition and compare it to its theoretical lifespan. This enables predictive maintenance and helps avoid unexpected downtime.
More to read!
What is a hydraulic cylinder?
01.07.2025
Put simply, a hydraulic cylinder is one of the four key components in a hydraulic system. In these systems, fluid, typically hydraulic oil, is used..
Read moreAlternative drive concepts: opportunities for hydraulic cylinder manufacturers
18.02.2025
As Bauma 2025 approaches, the exhibition’s key focus on sustainability and innovation resonates deeply with the challenges and opportunities hydraulic cylinder manufacturers, like us at..
Read moreSustainable construction from a hydraulic cylinder manufacturer’s perspective
22.01.2025
The construction industry is undergoing a transformative shift toward sustainability, driven by a growing awareness of its impact on the environment and the pressing need..
Read moreRevolutionizing heavy machinery with Hydroline LEO
05.12.2024
The future of heavy machinery is not just about size or power, but also about intelligence, precision, and sustainability. Hydroline’s LEO technology is driving this..
Read more