Hydraulic cylinder assembly briefly
At Hydroline, our experts meticulously handle the hydraulic cylinder assembly process, a task that demands careful concentration and expertise. Before initiating assembly, each part undergoes a thorough cleaning and protective measures. The purity of components is scrutinized through daily sampling, employing gravimetric analysis to ensure cleanliness. Logistics personnel ensure the availability of necessary components.
The assembly process unfolds systematically:
- Seal Placement: Seals, bearings, and snap rings are positioned.
- Rod Assembly: The piston and cylinder head are attached to the rod.
- Seal Oiling: Seals around the piston and cylinder head are oiled.
- Tube Installation: After assembling the rod with every component, the package is ready for tube installation.
- Cleanliness Priority: Cleanliness remains a top priority throughout, with surfaces kept clean and wiped when necessary.
- Visual Inspection: The tube undergoes visual inspection with internal light, then attached horizontally to an installation bench with proper oiling.
- Rod Insertion: The rod is carefully slid inside the tube with the piston end first.
- Torque Adjustment: Torque is set as per customer requirements.
- Final Touch: After assembly, bearings and grease nipples are installed.
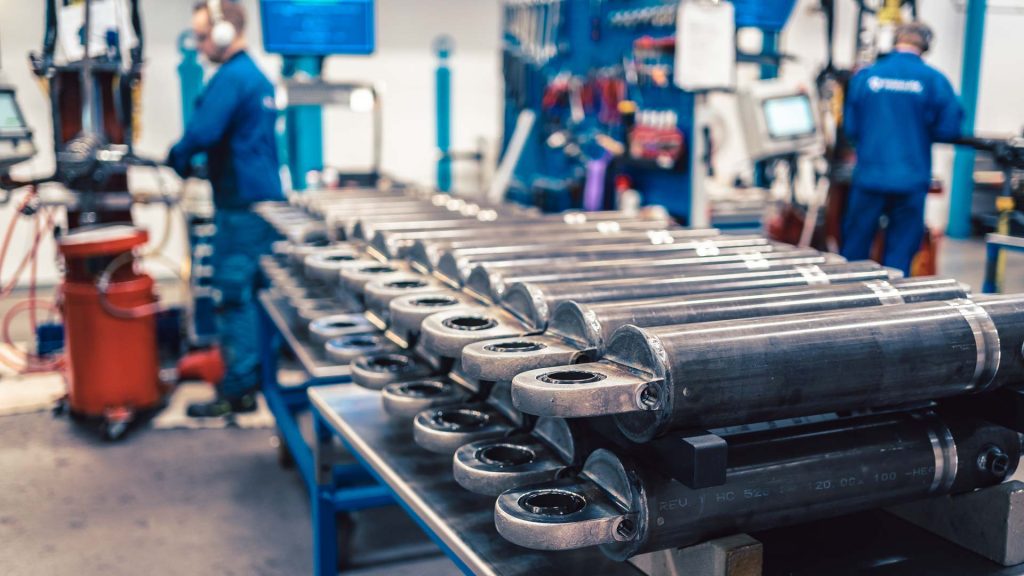
While the basic assembly idea remains consistent, variations arise due to different valves, sensors, and customer-specific features. Assembly times vary depending on components and cylinder size. Larger cylinders require specialized lifting and torque equipment.
The assembly process relies on carefully drafted drawings and working instructions, crucial for maintaining quality and effectiveness. These documents provide information on locking materials, torques, and test pressures. Standardization is achieved through working instructions, ensuring consistent quality.
Post-assembly, cylinders undergo proof testing, usually followed by valve installation. This approach addresses the “dry” condition post-assembly, where air remains inside. Valves are installed after the proof test to prevent air entrapment, avoiding potential security risks and accidents during pressurized oil pumping.
Commitment to continuous improvement
Throughout the process, our assemblers prioritize meeting customer expectations, ensuring the cleanliness and careful inspection of each part. In recent years, significant changes have been implemented, renewing the production process for enhanced cleanliness and efficiency. Our commitment to continuous improvement aligns with our goal of providing customers with even better service.
If you wish to read a more comprehensive blog post about hydraulic cylinder assembly, you can read it from the link below: