How to design a hydraulic cylinder?
How to design a hydraulic cylinder? The hydraulic systems date back as far as over 4,000 years ago in Ancient Egypt. They initially applied the principles of fluid hydraulic to the complicated canal systems used in watering. Other civilizations, including the Greeks and Romans, used the same basic principles to develop water-powered structures and devices like the water clock and water wheels. Since then, the fluid power universe has become a little more complicated. Fluid power has been used for Centuries to create energy to generate movement and force.
The fast-paced evolution of hydraulics has led to a firm and efficient hydropower form that we still use today. Modern hydraulic cylinders are complex devices incorporating various individual components in multiple dimensions, configurations, and materials. Hydraulic power is now all around us and is used in everyday life. The hydraulic system is up to ten times more potent than any electric motor, making it extremely helpful when lifting and moving heavy items. The precise mechanics make it a safer alternative than electricity alone, and therefore it is a better choice for human usage. The massive list of benefits has led to the popularity and many uses within construction, mining, marine, shipping, and manufacturing industries.
For many design engineers, playing it safe by over-engineering cylinder specifications has become a prudent habit in the presence of ever-improving cylinder technologies. We will clarify why less is sometimes more for complex hydraulic systems while identifying some of the many factors to be considered when designing hydraulic cylinders.
A complicated process
Nowadays, in the industrial manufacturing environment, hydraulic cylinders are complex devices that contain a wide range of components available in a large number of sizes, configurations, and materials. When it comes to complex hydraulic systems, cylinder specification can be a balancing act for design engineers — as each design factor influences one or more of the many other design details that need consideration for the application.
The hydraulic system design guidelines like NFPA and ISO exist, but many industries have developed their customized guidelines. Some cylinder manufacturers offer a vast extent of performance capabilities for standard components, minimizing the need for customization — however, exceptions to this remain. Working with an experienced engineering manufacturer can help to navigate and expedite the design process.
In this blog, we’ll look at some of the many factors that need consideration when specifying hydraulic cylinders and simplifying the process.
Design criteria in hydraulic cylinders
Designing hydraulic cylinders requires many factors involved in the process. Ignoring any of these critical steps in the design process could increase the possibility of a design mistake. Hydraulic cylinders have many different working conditions, and that affects the design criteria. For example, the cylinders used in the mining & construction machines versus forestry have other design criteria in terms of materials used.
There are a few main variables that should be taken into account while designing a hydraulic cylinder. What to consider when specifying hydraulic cylinders?
Working conditions
In general, it’s essential to consider the working conditions – where and what – the hydraulic cylinder is designed to do and what kind of load it has to endure. For example, challenging working conditions could be a corrosive environment, falling rocks in the mining industry, or high working cycles causing welding fatigue and shortening seal life span. For example, the requirements are different if the cylinder is mounted on the driving machine’s base, where stones and stumps may hit the cylinder compared to a cylinder mounted on a shelter inside the boom. If the cylinder is working underwater conditions, how to prevent the water from entering the cylinder fluid? These are examples that the designer needs to take into account when designing a hydraulic cylinder.
Stroking distance requirements
It is essential to consider the system pressure when choosing suitable design elements and cylinder parts. The stroke length can be a problem even at distances shorter than 3m. The thickness of the shaft is usually not determined by the impact but by force required. Long-stroke lengths may require choosing a larger cylinder size class than what the pressure levels would evaluate. In other words, even if the Ø50 / 30 cylinder is sufficiently generating, it may be necessary to select Ø63 / 40 so that the cylinder does not buckle. The best way to practice hydraulic system performance optimization is by comparing the positive effects to any potential negatives.
Temperature
Considering the working conditions in terms of temperature – high temperatures like desert conditions or icy weather conditions with more than – 30 Celsius Degrees affects the fluid choices used in the system. Hydraulic cylinder systems using standard components can meet application temperatures over 200°C and under -50°C degrees. These temperatures affect both the “hard” and “soft” design components of cylinders. Applications working in extreme temperature spectrum conditions require individual components’ best performance in short- and long-term expectations.
Speed
When the designer chooses suitable cylinder parts, he needs to consider the system sliding speed. The definition of – excessive speed – can vary from one design engineer to another. As a good rule of thumb, standard hydraulic cylinder seals can easily handle rates up to 0,5 meters per second. For higher speed applications, a standard low-friction seal is the better choice. What is essential to understand is what you gain in one aspect of performance; you lose in another. The greater the fluid velocity, the higher the liquid temperature, so when opting for speed-increasing customizations, it is essential to consider the impact of higher temperatures on the entire hydraulic system. In some hydraulic systems, oversized ports may eliminate escalated temperature concerns.
Capacity
Some applications, such as mining and construction machines and automotive manufacturing, require heavy-duty systems. Our cylinders typically have a working pressure of 200 to 350 bars. Testable pressure limits for our production are typically 420 bars, in special cases up to 700 bars.
Mounting styles
Every mounting type comes with benefits and limitations. There are three categories of mounting styles. Fixed and pivot styles can absorb forces on the cylinder’s centerline and typically include medium-duty and heavy-duty mounts to accommodate thrust or tension. The third category of selected types allows the entire cylinder to be supported by the mounting surface below the cylinder centerline, rather than absorbing forces solely along the centerline.
Cylinder bore size
The amount of push or pull force required is one of the variables what determines the bore size needed. Bore size is then related to operating pressure.

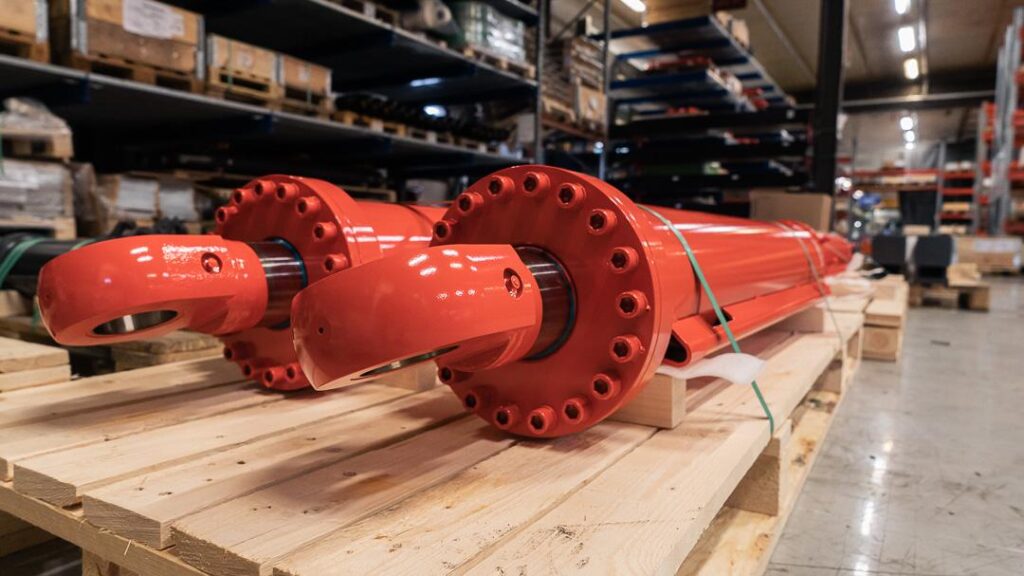
The hydraulic cylinder design process at Hydroline
The initial data in the design process
Like any other design process, the process of hydraulic cylinders starts with a customer request. The design process begins with the designer’s information about the cylinder and the requirements in advance. The more specific and comprehensive the provided information is, the better because the cylinder’s conditions are a significant part of the design process.
At Hydroline, we ensure that each hydraulic cylinder is a unique system designed according to the customer’s specific needs. Here we’d like to highlight an example process guideline we follow for each cylinder design process.
Here we have summarized the questions you need to keep in mind when choosing the right kind of cylinder for the purpose:
- Where will the cylinder be used?
- How are the conditions, and what additional requirements are needed?
- What kind of hydraulic pressure will there be in the cylinder?
- How heavy will the load be? Is a load holding needed?
- The required maximum weight capacity?
- How much accuracy and control is required?
- How will the cylinder be used, and how much space is needed?
- How is the cylinder mounted?
- What stroke is required?
- Does the application need to pull and push?
- What material requirements does the cylinder have? For example, acid-resistant, corrosion-resistant, stainless, or aluminum?
- How plane is the contact point with the saddle? Are tilt saddles needed?
You can also read our previous blog post about hydraulic cylinder’s initial data from here.
![]() | ![]() |
Design factors for hydraulic cylinders
Design factors are an essential part of the design process for hydraulic cylinders. The designer needs to consider the balance between each positive effect against possible negative one to gain the best possible performance. Each design factor influences the other design factors, and the designer’s main task is to find the balance between those. Here we give a closer look at those factors.
At Hydroline, we quite often use the crane standard EN 13001-3-6 for specific applications. As an experienced engineering manufacturer, we can expedite any custom design hydraulic system.
1. The final operating environment
One essential piece of information concerning cylinder design is the environment where the cylinder will function. It’s the base for the material choices used in cylinders. These cylinders may work in harsh environmental conditions such as damp or sea areas, under great strain, and impurities. The temperatures may differ from -50 C° to + 200 C° degrees.
What does it mean in practice? For example, if the cylinder will function in harsh weather or environmental conditions, the material choices need to be selected. The mining conditions may require extra duration for seals and metal parts against the work environment’s acidity. Or the high temperatures and dust in desert conditions. Possibly also cold and wet weather conditions in the Arctic environment. Information about these operating environment factors is also needed for the cylinder’s finishing; like a painting, the surface can endure the demanded circumstances. The designer’s other details are the operating pressure and external forces when designing a cylinder.
2. Lifetime goal – The strength calculation
A vital part of the hydraulic cylinder design process is the strength calculation.
The strength calculations are performed at a certain pressure level, and the number of cycles can be seen as a result. If the desired result isn’t achieved, the plans are fine-tuned, the structures are reinforced and recalculated. The strength calculations must be able to be taken into account already at the design stage. The designer typically looks at safety factors at maximum pressure, fatigue life, and buckling. Extra information such as the hydraulic diagram of the machine and cylinder’s using purposes is an excellent aid for the design process.
3. Functions and features of a hydraulic cylinder
When starting the design process, the designer needs initial data and specific information on the functions and parts required for the hydraulic cylinder. Many applications might seem like they need special features, but most of them only need slight design modifications. This fact simplifies the process and reduces design costs. However, the functionality and features of hydraulic systems may differ significantly depending on their operational purpose and the conditions they will be used. For example, two seemingly similar cylinders might have been designed for completely different users and create different amounts of force depending on their application.
4. Installation environment
The 3D model of the hydraulic cylinder gives accurate information about the environment in which the cylinder needs to act. The designer gets a clear picture of the machine and the space required for the cylinder functions. The information about the machine’s cylinders’ connection sizes and locations helps the designer get a full picture of the cylinder environment. The 3D model most often shows the cylinder’s connection sizes and the sites provided by the customer. The customer gets the 3D model to review the product in the operating environment. In some cases, we receive the 3D model of the application, but usually, the customer does the review themselves.
5. Cylinder’s oil flow, speed, and sliding distance
The cylinder movement speed (m/s), the oil flow (l/min), the sliding distance (m or km), and the stress accumulation are vital parts of the cylinder lifetime. All the information helps the designer to choose the right kind of seals and tube materials. How much force needs to be created is an essential part of the cylinder’s functionality.
The design engineer defines excessive speed. Usually, the standard hydraulic cylinder seals can easily handle speeds up to 0,5 m/sec. Most often, the best choice for high-speed applications is standard low-friction seals. An important notion is what you will gain in one aspect of performance you will lose in another. The higher the fluid velocity is, the higher the liquid temperature will be. When pursuing higher speeds, it is essential to consider how the higher temperatures will affect the entire hydraulic system. For example, over-sizing, the ports may eliminate concerns over higher temperatures in some hydraulic systems.
In Hydroline, we have solved these cases when there’s not enough information available about the cylinder’s actual operation with LEO (Lifecycle Efficiency Online). The use of cylinders can be measured with LEO, and the data turned into a readable form. LEO specifies the information – what affects the cylinder in the act and how much force the cylinder needs to endure, and that estimates the possible lifespan.
However, we want to highlight the most important single thing in the whole design process: listen to the customer’s needs and offer the best possible product and service.
6. Test requirements
In most cases, when a customer orders a hydraulic cylinder, there will be needs for hydraulic cylinder tests. These tests are often related to critical safety standards. These tests guarantee that the cylinder meets the actual machine’s safety standards and all the requirements have been taken into account. The cleanliness of the cylinder and the cylinder fluids, the fatigue measurements are examples of the test requirements. The flawless operation of the cylinder is critical for the entire system and operational safety.
The detailed information will be handled by the hydraulic cylinder manufacturer as well. This information is, for example, the packing requirements, dispatching, and cylinder marking. Hydroline’s designers are ready to exceed the customer’s needs and create hydraulic design systems that function beyond expectations.
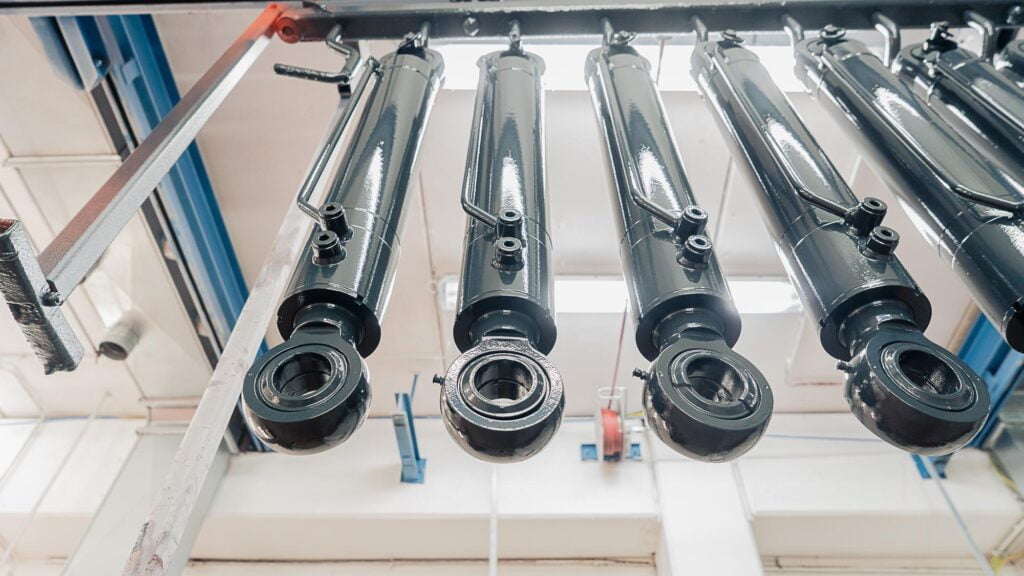
The hydraulic cylinder design process
The Hydroline main business is the manufacturing of hydraulic cylinders. The development of new designs by customer requests and the ramp-up of these applications is the core business. The technological development and excellent customer service create a strive to grow better and faster and pave the way for our international growth.
The outlined design process enables us to serve our customer needs better by offering customized cylinder development, technological advancement, a quick and efficient production process, and testing for the hydraulic cylinders we produce.
Hydroline New Product Development (NPD)
The Hydroline New Product Development (NPD) process stands for a series of products that haven’t been manufactured before at our factory. The NPD process starts with a customer needing a completely new machine that requires one or multiple cylinders.
As multiple new cylinders are needed, we handle the process as a complete set of new product families. We divide the new products into groups or product families by the features, and the whole production process will be more efficient.
The NPD process team consists of professionals from various departments of our organization: sales, production, sourcing, design, and quality. This team makes sure that the production process will be implemented correctly throughout the process. Hundreds of new products go through this process yearly.
The new product development in detail
Production plan and manufacturing tools – As the customer has approved the design, materials, and price, our engineering department starts making more specific production plans. They make sure we have all the needed tools available at our factory. For example, we need to be sure we have the right kind of tools and expertise for machining. Sometimes we need to write down new instructions if some part of the manufacturing process is implemented in a completely new way. Our production needs to know what requirements there are in the manufacturing. Our engineering department also designs the production flow and phasing for the output of each product. They ensure that the new products go through our products in the right way.
Production – The order desk takes care of planning the production, checking that the needed capacity is available, and planning the production process schedules accordingly. Our order desk handles all our orders and communicates with our customers about the timetable of new products.
Purchasing materials and components – After the product planning phase, our purchase team starts purchasing the needed materials. Suppose the new product requires components with extended delivery time (such as sensors, certain materials, or specific valves). Our sourcing department defines the sourcing channels for each element according to which our purchase team makes the actual material acquisition. Our purchase team also takes care that the needed materials and components arrive in time and the work does not get delayed.
Quality requirements – The Hydroline quality team plays an integral part in the whole process. Their main initiatives are quality documentation and ensuring the final products meet the customer requirements. The quality team provides the following things:
- The production flow – The manufacturing steps required for manufacturing.
- Failure Modes and Effects Analysis (FMEA) – FMEA offers a systematic, proactive method to evaluate a process to identify where and how it might fail.
- The FMEA process – The quality team, assesses the relative impact of different failures to identify the parts of the process that are most in need of change.
- Monitoring working instructions – The quality team controls if any instructions need to be modified or different procedures assembled for the process.
- Documentation – The quality team creates the measuring documentation templates, measures supplier components, goes through the measurement protocols to ensure the supplier components are according to specifications.
- Testing – The quality team carries out all the tests and provides test reports with a sample product of a new cylinder model to the customers.
If the customer wants to follow the production process, the quality team can arrange a process audit. Our primary target in Hydroline is to create products that meet our customer’s needs, and everything we produce is according to the requirements. We want to nurture our customer relationships with excellent service and outstanding products. We aim to create a world-class process that creates customized products efficiently, flawlessly to meet international growth needs.
Hydraulic technology in a constantly changing industrial environment
There are vast amounts of unique applications available with many conducive hydraulic cylinder design components in modern hydraulic engineering. Hydraulic engineering can metamorphose into a new evolution with its integration with new technologies. Electronic control and electromechanical power transmission play a considerable part in this. Hydraulic integration into electronic technologies will also create possibilities in the IT consumer world. There is still room for hydraulic power in a continually developing industrial environment in the future. Hydraulics offer distinct advantages, such as having high power density, making the technology a good enhancement for most modern machinery.
As we continuously strive towards growth, we want to serve our customers efficiently by offering them a well-planned process that quickly produces their cylinders. As technology, customer requirements, and economics evolve, we need to stay up with them and meet our current customers’ needs by continually developing our product base and replacing outdated products with new ones.
In conclusion, the hydraulic cylinder design process can be time-consuming and complicated. Partnering with an engineering manufacturer experienced in hydraulic system design such as Hydroline early in the design process can save time and money and ensure reliable system operation and long life span.